Weibold Academy: ELT pyrolysis – a remarkably accurate vision from 1993
Weibold Academy article series discusses periodically the practical developments and scientific research findings in the end-of-life tire (ELT) recycling and pyrolysis industry.
This article is a review by Claus Lamer – the senior pyrolysis consultant at Weibold. One of the goals of this review is to give entrepreneurs in this industry, project initiators, investors and the public, a better insight into a rapidly growing circular economy. At the same time, this article series should also be a stimulus for discussion.
For the sake of completeness, we would like to emphasize that these articles are no legal advice from Weibold or the author. For legally binding statements, please refer to the responsible authorities and / or specialist lawyers.
Author's foreword
Sometimes it makes sense to periodically sift through your personal library (even though that's primarily done electronically these days). When you browse around, some things come to light that are worth not forgetting, such as a conference paper that was published exactly 30 years ago in August 1993.
“A multiple-product approach to the processing of used tires” (Michal A. Serio, et al., 1993) is a remarkably accurate vision of chemical recycling of end-of-life tires (ELTs), as it is experiencing a boom in the last few years.
The authors presented their well-founded proposals for sustainable recycling of ELTs through pyrolysis at a conference of the American Chemical Society (ACS Division of Fuel Chemistry) in the USA. About 20 years later, namely in 2011, the United Nations Environmental Program (UNEP) within the framework of the Basel Convention (191 signatory states) approved the chemical recycling of ELTs by pyrolysis as Environmental Sound Management (ESM). This classification was subsequently also included in the European regulations.
In this exposé of the remarkably visionary work, the original text is quoted and only occasionally an outdated term is replaced by the one used today. Replacements and comments are in Italic. This paper by Michal A. Serio and colleagues could just as well have been written today.
Abstract (shortened original)
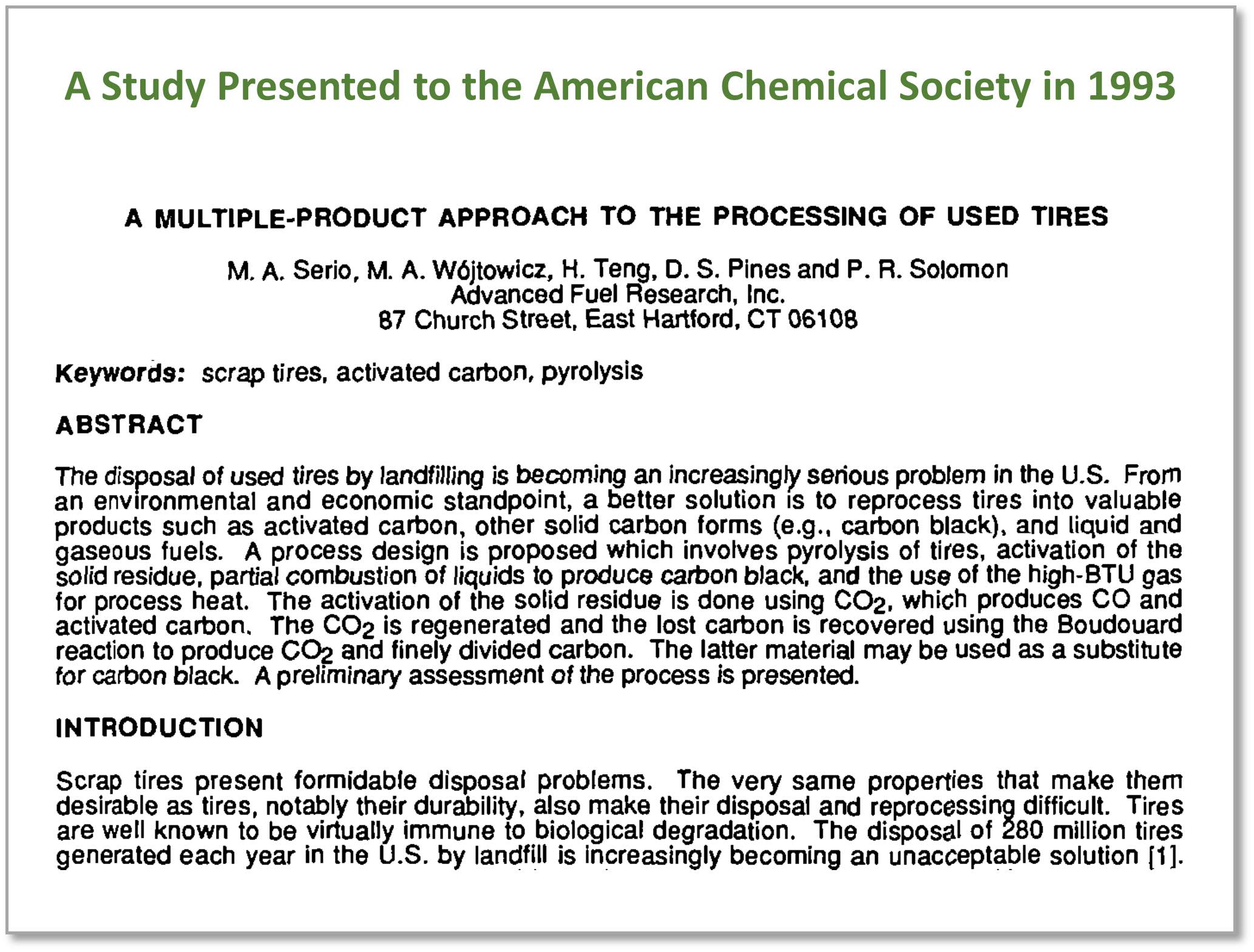
Abstract and Intro from Study on ELT Processing, August 1993.
The disposal of used tires by landfilling is becoming an increasingly serious problem in the US. From an environmental and economic standpoint, a better solution is to reprocess tires into valuable products such as activated carbon, other solid carbon forms (e.g., carbon black), and liquid and gaseous fuels. A process design is proposed which involves pyrolysis of tires, activation of the solid residue, partial combustion of liquids to produce carbon black, and the use of the high-BTU gas for process heat.
About the challenges
Scrap tires (ELTs) present formidable disposal problems. The very same properties that make them desirable as tires, notably their durability, also make their disposal and reprocessing difficult. Three features underlie the problem of converting used tires and other waste polymers into useful, marketable products. The first problem is the low level of understanding of the chemistry and physics of tires during thermal degradation. Secondly, even if the thermal degradation processes were well understood, the decomposition process would have to be monitored carefully to maintain product quality. The tire feedstock varies with time, and the process engineer must be able to monitor reactions and respond to changing conditions as necessary. Finally, the technology must produce a high yield of a product with a viable market. The best solution to disposing of waste tires is to develop a chemical process to convert the tires into another commodity material.
[Author’s Note: The development of pyrolysis technology in the last 10 to 20 years, but especially in the last 5 years, has produced an enormous number of scientifically based findings on the chemistry and kinetics of pyrolysis technology. At the same time, technology in general, and in particular the degree of automation, has developed significantly, so that technically mature, environmentally friendly, and safe technologies are available today.
In addition, in recent years there has been great interest in sustainable pyrolysis products (TPO and rCB), for which in some places premiums are already being paid above the market prices of the fossil products to be substituted].
The proposed solution for ELTs in 1993
The proposed solution is to thermally reprocess the used tires into activated carbon, other solid carbon forms (e.g., carbon black, graphite, or carbon fibers) and/or liquid and gaseous fuels. The process is based on pyrolysis of tires and the key to its successful development is understanding and controlling the chemistry of low temperature carbonization so that the yield and physical properties of the products can be optimized.
Pyrolysis has been widely used for converting solid fossil fuels, e.g., coal, into liquid and gaseous hydrocarbons, a process which results in a solid char residue. Used automotive tires contain polymeric aromatic structures which are similar to those of coal in some respects. Not surprisingly typical elemental compositions of both materials are also similar (rubber -- 88% C. 8% H, 2% 6: 0.5% N, 1.5% S; and coal -- 82% C..5.5% H, 8% 0, 1.7% N, 2.4% S). Coal pyrolysis has been extensively studied but investigations of tire pyrolysis are rarely reported in the open literature. [Author’s Note: The latter has changed significantly as hundreds of scientific studies are now available on virtually all aspects of tire pyrolysis.]
In most cases, tire pyrolysis studies were performed under inert conditions. Pyrolysis may also be carried out in mildly oxidizing atmospheres, such as steam and carbon dioxide, to improve the quality of pyrolytic products. [Author’s Note: This aspect has hardly been tested with modern technology to this day.]
Tire pyrolysis experiments have usually been conducted in the 773-1 173 K (500 – 900°C) temperature range. Similar to coal pyrolysis, the principal products from thermal degradation of tires are gases, liquid oils, and solid carbon residues (raw rCB). The following yields of tire pyrolysis are typical (on an as-received basis): 33-38 wt.% char (raw rCB), 38-55 wt.% oil (TPO), and 10-30 wt.% gas. The product yields are affected by the pyrolysis conditions, such as pyrolysis temperature and heating rate.
[Author’s Note: Since nowadays there is an enormously high demand for TPO (higher process temperature decreases the yield of oil) and also for reasons of the energy balance, etc., process temperatures in the range of 450 to 600°C are used in modern plants.]
Pyrolysis products as seen in 1993
Gas Analysis -- Gases produced from tire pyrolysis are mainly hydrogen, carbon dioxide, carbon monoxide. methane, ethane, and butadiene, with lower concentrations of propane, propene, butane, and other hydrocarbon gases. […] The fuel gases produced during pyrolysis can be used to provide process heat for the pyrolysis […]. Preliminary estimates show that the process […] will be self-sufficient from an energy standpoint.
Oil Analysis -- The yield of oil from tire pyrolysis is high (~50 wt. % of initial tire rubber), reflecting the potential of tire rubber to act as a substitute for fossil fuel and chemical feedstocks. The oils have high aromaticity, low sulfur content, and are considered relatively good fuels. The molecular weight range for the oils is up to 1600, with an average molecular weight between 300 and 400. Infrared analysis of the oils indicates the presence of alkanes, alkenes, ketones or aldehydes, aromatic, polyaromatic and substituted aromatic groups. The derived oils may also be an important source of refined chemicals because it has been reported that they contain high concentrations of valuable chemical feedstocks, such as benzene, toluene, and xylene.
[Author’s Note: This is a remarkably accurate prediction of today's fields of application: The biogenic content (from the natural rubber in the tire) of tire pyrolysis oil (TPO) is recognized in the UK as a development fuel under the Renewable Fuel Obligation (RTFO), and the German large-scale chemical industry (BASF) successfully uses the TPO to produce sustainable base chemicals (ChemCycling®). Currently, demand for TPO is virtually unlimited.]
Carbon Residue Analysis -- The carbon residue (raw rCB) could become a marketable product if its properties were similar to those of manufactured carbons.
[Author’s Note: In the meantime, the suitability of replacing commercial carbon black (CB) with sustainable recovered carbon black (rCB) has been scientifically and practically proven. Leading tire manufacturers have formed alliances and are promoting the use of rCB in tire rubber production. In many applications in the rubber and plastics industry, rCB is already a standard application nowadays. Furthermore, rCB is being standardized by the ASTM Committee D36.]
The simultaneous production of valuable solid products and gaseous and/or liquid fuels from what is currently a waste material would make tire pyrolysis economical if a large supply is readily available. This situation exists in many regions of the U.S. [Author’s Note: … as well as in most regions of the world, since today only around 3% - with a strong upward trend - of the ELTs produced each year yet find their way into chemical recycling.]
A concept for the carbon black industry (from 1993)
The oils resulting from tire pyrolysis can be used to produce carbon black since their properties are known to be similar to those of the petroleum fraction used in carbon black production. In the oil-furnace process, a highly aromatic feedstock is converted to carbon black by partial combustion and pyrolysis […].
The conversion of the oil stream to carbon black is an […] attractive option for a number of reasons: (1) the value of the solid product is higher than any possible fuel uses; (2) little or no upgrading of the material is required; and (3) since carbon black is required to make tires, the production of carbon black from the oil is a form of tire recycling and is more practical than trying to recover the original carbon black.
[Author’s Note: This is also a remarkably accurate prediction of today's fields of application: practically all major carbon black producers are intensively promoting the replacement of fossil carbon black feedstock (CBFS) with sustainable TPO. The EU-funded BlackCycle® project is just one example.]
Conclusion (shortened original)
The proposed technology has the potential to convert an unmitigated waste stream of tires into marketable products (activated carbon, Boudouard carbon and carbon black). Tire-derived activated carbons could be used, for example, in waste-water treatment, stabilization of landfills and in the recovery of organic solvents and vapors. The Boudouard carbon may have a variety of uses which are yet to be explored; they include the manufacture of colorants and lubricants. The liquid stream can be utilized in the production of carbon black and/or fuel oil. The oil derived carbon black can be reused in tire manufacturing, which forms a recycle loop for this material. Since the typical feedstocks for activated carbon and carbon black are either coal or petroleum, the proposed technology would obviate the need to deplete these resources. The process allows a high degree of flexibility in the relative amounts of each product to reflect changes in the feed stream and market conditions. Another advantage of the system is the production of both activated carbon and carbon black from used tires, with inorganic material ending up in the product with a high tolerance for this.
[Author’s Note: Nothing more needs to be added here.]
Source: Serio, Michael & Wójtowicz, Marek & Teng, H. & Pines, David & Solomon, P. (1993). A MULTIPLE-PRODUCT APPROACH TO THE PROCESSING OF USED TIRES. Download available here or here.
Weibold is an international consulting company specializing exclusively in end-of-life tire recycling and pyrolysis. Since 1999, we have helped companies grow and build profitable businesses.