Gradeall International introduced its new OTR tyre cutting equipment
Gradeall International – a renowned manufacturer of tyre bailing and end-of-life tyre recycling equipment from Northern Ireland – reports about the recent addition cutting equipment to its OTR Tyre Cutting Range.
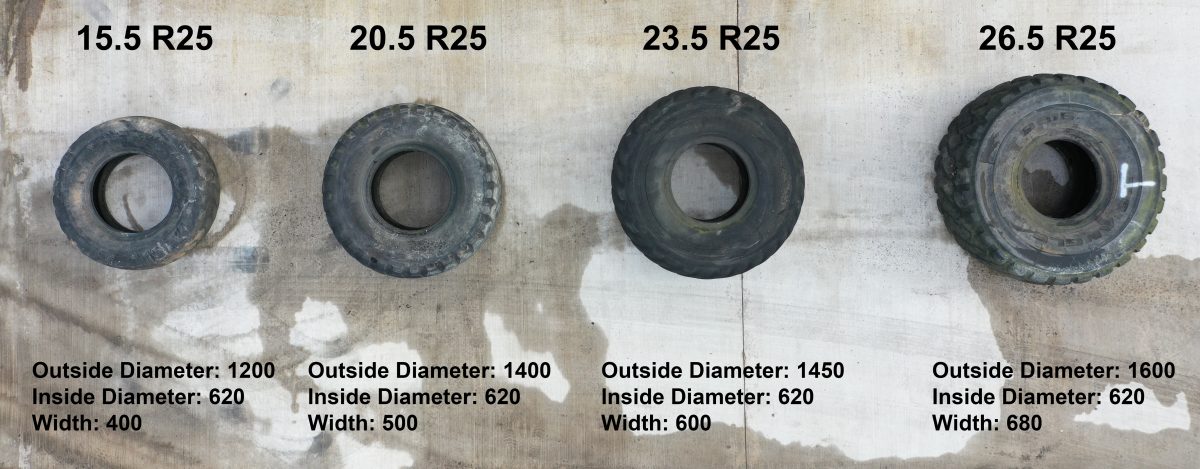
A sample range of the OTR tyres that can be cut with this equipment | Photo Gradeall International.
To address major challenges in the domain of off the road (OTR) tyre recycling, Gradeall have developed a new 3-pronged solution, which enables to effectively cut the OTR tyres and mitigate costs.
Gradeall reports that its team developed an affordable range of machines for dealing with these tyres. This range of OTR tyre recycling machines consists of:
- OTR Splitter
- OTR Sidewall Cutter
- OTR Shear
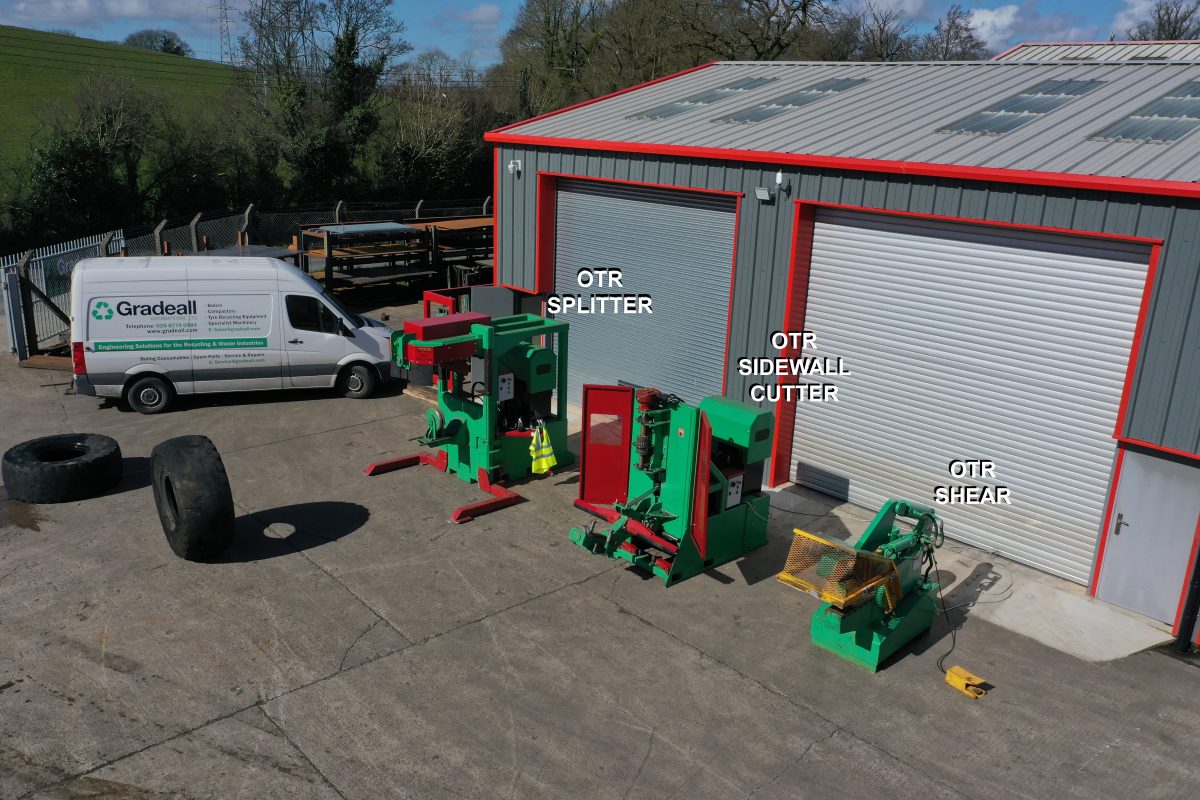
The 3 Machines in the Gradeall OTR cutting range | Photo Gradeall International.
Gradeall’s team pinpoints that the current problem in OTR tyre recycling is that these huge tyres take up a lot of space and are very heavy at approximately 600 kg per tyre making them take up a lot of space, they are impossible to move by hand and costly to transport due to low amount of material fitting on a trailer.
Using the Gradeall OTR cutting range these large tyres can be cut down into easy to manage segments weighing under 25Kg which means they can be lifted and moved around by anyone. These segments can be baled, shredded, sent for pyrolysis or any of the further recycling methods that are available to conventional tyres.
OTR tyre cutting process
The video below demonstrates how Gradeall’s equipment cuts OTR tyres into manageable and easily transportable pieces.
OTR tyre cutting equipment by Gradeall International | Video: Gradeall's Youtube channel.
Firstly the tyre is brought to the OTR Tyre Splitter which cuts the tyre in half along its tread section, at this stage any water or debris inside the tyre will fall out of the tyre. The tyre is now in two halves.
The second stage is to bring the halves of the tyre to the OTR Sidewall Cutter, this machine cuts the sidewalls out of the tyres, isolating the bead section (it is the thick bead section which typically causes the most problems for shredders).
It is possible to cut the sidewalls twice to give a ring of sidewall without any bead and a small sidewall cut close to the bead itself.
The final stage is to use the OTR Shear to cut the tyre down into smaller segments, the tread sections first which are the easiest to cut. This is followed by the sidewalls; the shear is sufficiently strong to cut through the bead of these tyres. Even when cut in half they are now much easier to handle.
It is entirely at the discretion of the operator how small to cut the segments of the OTR tyres, sub 25 kg pieces are optimal as this means that they can still be moved easily by hand.
Gradeall has had success in baling these OTR tyres, and in-house testing found that it was possible to deal with 6 OTR tyres per hour. While it is still a labour-intensive process it provides the market with a viable and affordable way to deal with these tyres. Gradeall as with the original sidewall cutter will continue to develop this system with the help of customer feedback to refine the process in order to make it as streamlined as possible. To learn more about the tyre baling process watch the video below:
The all-new Gradeall tyre baler conveyor designed to make baling of end-of-life tyres a more ergonomic process for baler operators | Video: Gradeall's Youtube channel.
To learn more about the company and its products, please navigate to Gradeall’s website or email to sales@gradeall.com.
Weibold is an international consulting company specializing exclusively in end-of-life tire recycling and pyrolysis. Since 1999, we have helped companies grow and build profitable businesses.