Weibold Academy: Production of Limonene by vacuum pyrolysis of end-of-life tires
The advantages of pyrolysis to tackle the world's growing disposal problem with end-of-life tires (ELT) in terms of a circular economy were described extensively in the last decade. Pyrolysis is a thermal process that converts organic rubber material into low molecular weight compounds such as pyrolysis gas, pyrolysis oil and raw recovered Carbon Black (ASTM 8178-20a). In contrast to the incineration of ELT, which is often condescendingly referred to as "thermal recycling" or „waste-to-energy“, pyrolysis does not destroy any raw materials, but breaks down the waste product into its chemical raw material components and makes them available for the circular economy. Fortunately, this is in the meantime confirmed by the great demand from the chemical industry for products from ELT pyrolysis.
Despite all the apparent simplicity of this thermo-chemical recycling process, the implementation practice shows that it is not a trivial process, and that the system technology and the product quality produced have a decisive influence on the economic viability of this emerging recycling route.
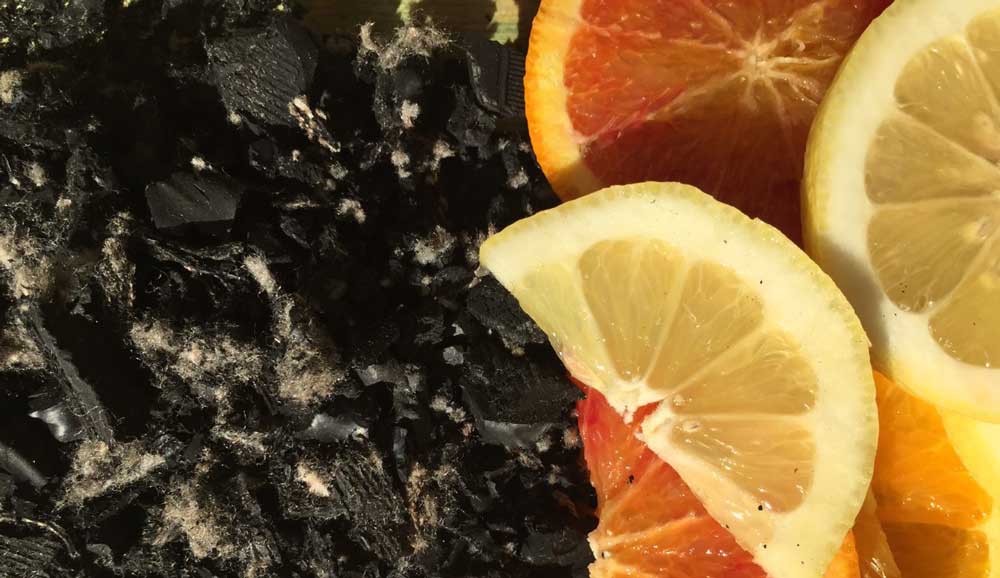
Photo by Weibold.
Tire pyrolysis oil (TPO) is currently the target of several research projects which examine its production, characterization, upgrading and implementation. Because of its renewable characteristics and its compatibility with crude oil, TPO fulfills the definition of dropin-biofuels established by Task 39 of the International Energy Agency. (CAMPUZANO et.al., 2021)
Furthermore, tire pyrolysis oil (TPO) is a potential source of chemical feedstock as it contains valuable chemicals like benzene, toluene and xylene (BTX), styrene, ethylbenzene and limonene. The latter is a high value light hydrocarbon used in the formulation of industrial cleaning agents, terpene resins and adhesives, fragrance in cleaning products and as an environmentally acceptable solvent. The presence of these various compounds could make ELT pyrolysis an excellent additional pathway for upgrading and recovery of valuable chemicals.
As the demand for limonene is mostly catered for by citrus-derived limonene (DANON et.al., 2015) supply of citrus limonene is subject to agricultural vulnerabilities and price volatility. Production and recovery of ELT derived limonene then become vital to close the potential limonene supply gap given the wide industrial use of limonene. (Ciriminna et. al., 2014; MULAUDZI, 2017)
Even if no prices for ELT-derived limonene can be determined yet, the currently known price range for citrus limonene between 8 and 25 USD per kilogram based on purity (MULAUDZI, 2017) shows an economically interesting perspective.
An Aspen Plus® simulation of a multi-step limonene separation process by distillation revealed that a limonene stream of 95 wt.% limonene purity, with an overall limonene recovery of around 95% could be achieved. (MULAUDZI, 2017) The separation system in this study consists of 4 distillation columns (main unit operations) and was based on the experimental work of Pakdel et al. (2001), which included compounds within around ±8 °C of the boiling point of limonene. Diethylene glycol (DEG) was introduced to remove most of the impurities, thereby obtaining a limonene stream of (minimum) 95 wt.% limonene purity as distillate. (MULAUDZI, 2017)
Vacuum pyrolysis is obviously preferable for limonene production as the faster removal of volatiles from the reaction zone prevents the secondary cracking reactions which would degrade limonene. The typically lower operational temperatures of vacuum pyrolysis also reduce the possibility of limonene degradation. Pakdel et al. (2001) found that vacuum operation improves the yield of limonene at the expense of aromatics due to the rapid removal of volatiles and the reduced pyrolysis temperatures (lower than 500°C), reduces the occurrence of Diels-Alder type of aromatisation.
MULAUDZI evaluated the economic feasibility of a 30 tons/day ELT to limonene process, producing limonene at a rate of 672 kg/day and a purity of 95 wt.%.
The sensitivity analysis showed that the process is most sensitive to changes in the cost of distillation columns (CapEx), limonene selling price, and the yield of limonene. In order to achieve 25% IRR for economic attractiveness, a maximum column cost of 2.5 mio US$, a minimum limonene selling price of US$10/kg, or a minimum limonene yield of 2.1 wt.% are required. To achieve a minimum IRR of 12% to ensure feasibility, a maximum column cost of 5.3 mio US$, a minimum limonene selling price of US$ 5/kg, or a minimum limonene yield of 1.1 wt.% are required.
Even if the proposed limonene recovery process from the tire pyrolsyis oil (and here from the BTX fraction) is technically and chemically no trivial project, the figures indicate a feasibility, provided this process can be integrated into an existing or planned pyrolysis plant with an annual capacity of (at least) 30,000 tons of end-of-life tires.
Do you want to lean more about pyrolysis and limonene? If so, please contact the authors of the article – Pavol Fehér and Claus Lamer.
Weibold's services
Weibold is the expert in tire recycling and pyrolysis consulting, who works with both new and established tire recycling and pyrolysis companies, waste management authorities and regulatory bodies since 1999 and helps them build successful businesses. Weibold has helped over 500 companies worldwide and has a truly global portfolio.
For more information about our reports, please visit our web shop or consider our consulting services.
Also, to learn how we can help you build successful pyrolysis business or help you design regional tire collection system, write us at sales@weibold.com or call +43 1 997 10 50.
Weibold is an international consulting company specializing exclusively in end-of-life tire recycling and pyrolysis. Since 1999, we have helped companies grow and build profitable businesses.