Radar to monitor tire wear developed by American engineers
American engineers have developed a sensor that can monitor tire wear in real time. It has a radar that emits millimeter waves and, thanks to wave reflection, determines the depth of the remaining tire tread depth with an accuracy of 0.68 millimeters. In addition, it is capable of detecting foreign objects in the tread. An article on development was presented at the MobiSys 2020 conference.
Besides indirect benefits of the system to tire recycling practices, there is a huge benefit of using such a radar by drivers themselves. Tires are one of the main factors affecting how a car drives on the road, handles and brakes. These parameters directly depend on the condition of the wheel: tire wear and pressure in it. In many countries, all new cars must be equipped with a tire pressure monitoring system that monitors pressure directly or indirectly and signals when one or more tires have dropped. To monitor the condition of the tire itself, either standard intervals (mileage after which it is recommended to replace tires) or visual inspection are used.
The radar system invented and presented at MobiSys by Akarsh Prabhakara, Vaibhav Singh, Swarun Kumar and Anthony Rowe.
Engineers from Carnegie Mellon University, led by Anthony Rowe, have developed a system that allows real-time monitoring of the condition of the tread: wear and the presence of foreign objects in it. It is based on an automotive radar that operates in the millimeter-wave range at frequencies from 77 to 81 gigahertz and was originally designed to detect obstacles. As conceived by the authors, the radars can be placed in the wheel arches. Also, during some of the tests, they placed it on a test bench near the horizontally located wheel.
The radar transmits signals, receives reflections and maps the depth of the tire surface. The engineers improved the original radar resolution in two ways. First, there are eight antennas in the radar, and this allows the signals from them to be summed to improve accuracy. Second, they used the Inverse Synthesized Aperture Radar (ISAR), which increases the resolution of the subject due to its movement. In this case, the authors used the rotation of the bus to increase the resolution, due to which the same elements of it reflect signals from different positions.
The limitation of the ISAR method is that the radar needs to know the angle of the wheel at every moment. For this, the developers used aluminum strips of a certain length, glued to the longitudinal grooves of the tread. Since the strips are of different and known in advance the length, the radar can at any time, by their location, determine the fragment of the tire that it is currently filming. In addition, the strips filter out objects stuck in the tread in the signal.
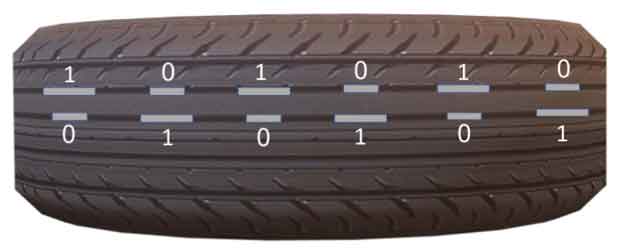
Glued aluminum strips in the tread grooves Akarsh Prabhakara et al. / MobiSys 2020
Engineers tested the operation of the radar at a tire changer, as well as during real trips by car, in one arch of which a sensor prototype was fixed. They first tested it on artificial surfaces with different types of obstacles that create vibrations of different intensities. Tests have shown that the accuracy in determining wear (the difference in height between the ridges and grooves of the tread) is 0.21 millimeters for low vibrations, 0.68 for medium and 0.73 for high vibrations. Tests on real roads with different surfaces have shown accuracy from 0.19 to 0.68 millimeters.
Articles is based on the research of Akarsh Prabhakara, Vaibhav Singh, Swarun Kumar and Anthony Rowe.
Weibold is an international consulting company specializing exclusively in end-of-life tire recycling and pyrolysis. Since 1999, we have helped companies grow and build profitable businesses.