Weibold Academy: Recovered Carbon Black emerging in the rubber industry
Weibold Academy article series discusses periodically the practical developments and scientific research findings in the end-of-life tire (ELT) recycling and pyrolysis industry.
This article is a review by Claus Lamer – the senior pyrolysis consultant at Weibold. One of the goals of this review is to give entrepreneurs in this industry, project initiators, investors and the public, a better insight into a rapidly growing circular economy. At the same time, this article series should also be a stimulus for discussion.
Introduction
This article deals with the question of whether the scientific recommendations for the development of new modification methods for upgrading recovered Carbon Black (rCB) derived from end-of-life tire (ELT) pyrolysis have not already been (partially) overtaken by industrial practice. This question does not mean that the extensive research on rCB is unnecessary. Quite the contrary! Past and new research results were and are of priceless value for the development of new ASTM approved characterization methods to be able to predict rCB performance in rubber applications in a practical and science-based manner.
A current scientific paper (just one example of many) published by Jiaxue Yu and colleagues (2019) stresses the "immediate significance" for the further development of modified rCB (ash purified and structure modified). These recommendations are undoubtedly valuable for special applications, for example as a replacement for the virgin CB as colour pigments, as energy storage material in batteries or as super capacitators (etc.). However, since the primary application is as (semi-) reinforcing agent in tires and other rubber products, such cost-intensive and complex modification methods appear neither objectively necessary nor economically viable.
The sustainable rCB has already made the leap into industrial practice and is making an important contribution to closing the loop in the tire and rubber industry. The essential prerequisites are good and consistent product quality, constant production quantities from several thousand tons per year (the more the better), as well as an adequate business strategy.
The rCB produced anyway must always meet the ASTM D8178 definition and must be free of steel wire and fabrics, intensive milled (to eliminate the hard agglomerates) and pelletized, and properly packed, stored and transported.
Need for new classification standards for rCB
The latest opinion which emerged from the Recovered Carbon Black Congress held in Berlin (May 2019) defines rCB as a new material rather then being a 1 to 1 substitute to virgin Carbon Black. That is undoubtedly correct, as rCB is a heterogeneous material, regarding not only the ash content, particle size, morphology and both surface chemistry and activity and the fact that rCB is a mixture of more than one grade of virgin CB. Besides, the presence of a variety of organic and inorganic additives also exacerbates the complexity of the pyrolysis process by producing new substances that didn’t exist in the rubber pyrolysis products. [YU et.al.; 2019]
Recovered Carbon Black is a complex mixture consisting of carbonaceous deposits and oils absorbed during the pyrolysis process, together with various organic and inorganic additives. [YU et.al.; 2019] Carbonaceous deposit, resulting from secondary reaction during the pyrolysis process, is probably the most unwanted characteristic as it covers the surface (char layers), leads to much rougher particle sizes and limits the performance of rCB to a certain degree. (In our next article, we will deal in detail with how this disadvantage can be almost eliminated through reactor design and process parameters.)
In general, the quality and yield of rCB depends on the tire composition as well as pyrolysis conditions.
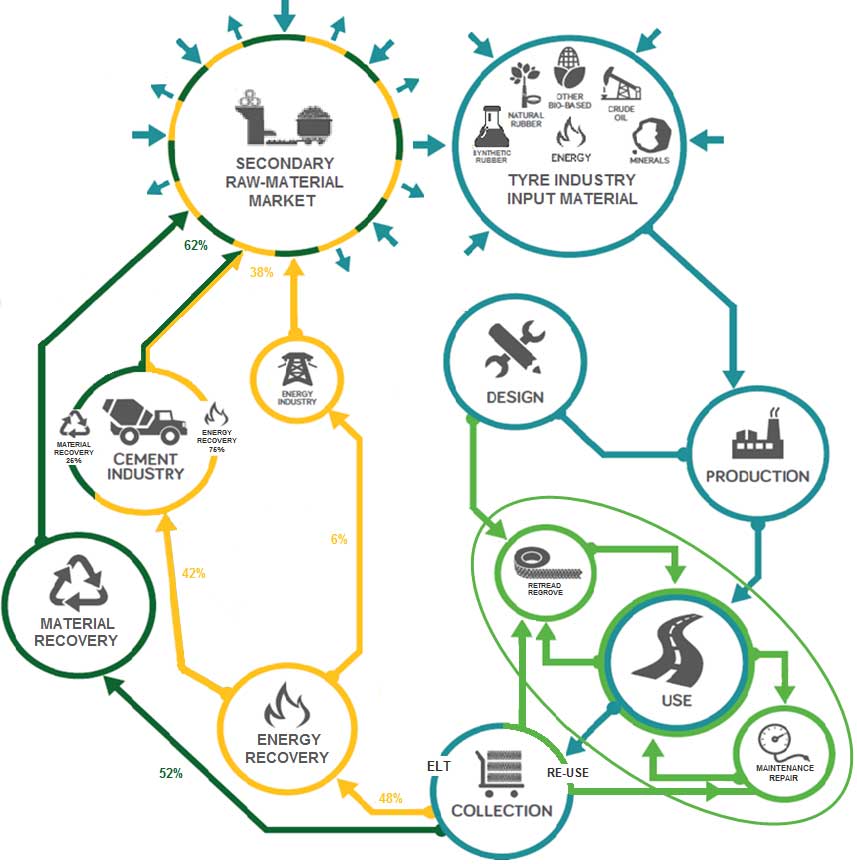
Continual use of resources – circular economy model for end-of-life tire recycling. | Graphics: courtesy of ETRMA.
Already considered superficially, it becomes clear that rCB is a new and very valuable nano-material that cannot only be characterized with traditional definitions and standards for virgin CB.
It is therefore most welcome that an ASTM commission (D36) is making intensive efforts to develop adequate standardization methods for the resource-saving and environmentally friendly rCB.
Industrial practice continues to advance in favour of rCB
Although there is still a lot of discussion on the research side about the differences between rCB and virgin CB, which is a positive and sensible process, the rubber and Carbon Black industry now seems to be increasingly relying on the advantages of using rCB.
Recent tests and scientific findings have shown that in carefully blending rCB with virgin CB, the same performance properties can be achieved.
MAKROchem, a specialist in CB based in Poland, has been researching rCB/CB blends and their performance in rubber compounds over the last three years while testing more than 30 rCB products available in the market. Mainly rubber compounds based on SBR and BR were analysed, establishing differences in the kinetics of vulcanization between rCB and N550 (attributed to the presence of mineral and organic inclusions). Nevertheless, in rCB/CB blends those differences are eliminated. During joint research conducted with its customers, MAKROchem learned that 10-20% blends of rCB/CB may be used in most rubber applications, while following a special industrial blending procedure. For specific applications, rCB content could be even increased to 30% or more. [TIRE TECHNOLOGY INERNATIONAL 2020]
A recently published study goes into even more detail and examines the effect of rCB from ELTs on the properties of styrene-butadiene rubber compounds (SBR). In this work, a commercially very successful rCB (ET black) was compared with N660 carbon black in SBR using ASTM testing and material recipes.
This extensive study shows that rCB (ET black) can replace 20% in N660 without much influence for SBR compounds (e.g.) in terms of tensile strength and tear strength.
Conclusion
Regardless of the question of whether and how one or the other process detail can still be perfected, for example by preventing secondary reactions during pyrolysis (there are always possibilities for perfection), it seems to be proven that properly produced and processed rCB can already be used as a sustainable substitute for N550 / N660 to the extent of approx. 20%.
This indicates an essential cut down in the carbon footprint of rubber and tire products, considering a rCB market potential of probably 2 million tons per year.
There is still a long way to go to achieve this, but the first big steps seem to have been taken.
Literature
- Yu, Jiaxue & Xu, Junqing & Li, Zhenchen & He, Wenzhi & Huang, Juwen & Xu, Junshi & Li, Guangming. (2019). Upgrading pyrolytic carbon-blacks (CBp) from end-of-life tires: Characteristics and modification methodologies. Frontiers of Environmental Science & Engineering. 14. 19. 10.1007/s11783-019-1198-0.
- Lai, Sun-Mou & Chu, Yun-Lan & Chiu, Yu & Chang, Ming-Chi & Hsieh, Tung-Yuan & Hsieh, Ming-Hsien. (2020). Effect of pyrolysis carbon black from waste tires on the properties of styrene–butadiene rubber compounds. Polymers and Polymer Composites. 29. 096739112090288. 10.1177/0967391120902882.
Weibold is an international consulting company specializing exclusively in end-of-life tire recycling and pyrolysis. Since 1999, we have helped companies grow and build profitable businesses.