Weibold Academy: rCB as a sustainable substitute for graphite and graphene
Weibold Academy article series discusses periodically the practical developments and scientific research findings in the end-of-life tire (ELT) recycling and pyrolysis industry.
This article is a review by Claus Lamer – the senior pyrolysis consultant at Weibold – and İbrahim Mutlay – consultant and materials scientist. One of the goals of the review is to give entrepreneurs in this industry, project initiators, investors and the public, a better insight into a rapidly growing circular economy. At the same time, this article series should also be a stimulus for discussion.
For the sake of completeness, we would like to emphasize that these articles are no legal advice from Weibold or the author. For legally binding statements, please refer to the responsible authorities and specialist lawyers.
Introduction
The tire waste recycling industry is transforming after 25 years of gradual progress. Traditionally, recycling focuses on mechanical processes to separate and recover rubber, steel, and fiber from End-of-Life Tires (ELTs), with applications developed for products like sports turf, civil engineering, mats, and even fuel for cement kilns. Despite these advances, a substantial amount of tire waste remains in landfills, contributing to soil contamination, or is incinerated overseas under poor environmental standards, emitting significant greenhouse gases. Additionally, tire manufacturers have limited use of (mechanically) recycled materials due to quality inconsistencies, making true circularity difficult.
However, new technological investments and growing sustainability demands catalyze changes that could disrupt the industry. These developments promise innovative recycling approaches that align better with corporate sustainability goals, potentially allowing for a larger proportion of tire waste to be reintegrated as high-quality, virgin-equivalent raw materials in manufacturing. This shift could lead to more sustainable and circular tire waste management practices across multiple industries. To meet ambitious sustainability targets, automotive, chemical, and tire production manufacturers must source high-quality recycled materials that match or surpass virgin material standards.
Achieving this requires products designed with circularity in mind and partnerships across industries to develop and test new materials collaboratively. For tire and rubber recycling, advancing chemical decomposition methods, like pyrolysis, is essential. Pyrolysis transforms tire waste into valuable materials like recovered carbon black (rCB) and pyrolysis oil, offering a sustainable alternative to fossil-based resources.
To support this shift, the tire recycling sector must scale production capabilities, address technical and engineering challenges, and establish rCB as a globally traded commodity.
Recovered Carbon Black (rCB)
Virgin Carbon Black (CB) ranks among the top 50 industrial chemicals in production capacity and is one of the most important (and irreplaceable) components of tires and technical rubber goods. CB is produced via incomplete combustion of heavy aromatic petroleum products such as fluid catalytic cracking tar (FCC), decant oil (DO), raw coal tar (CT), or ethylene cracking tar (ET). It is a unique and irreplaceable component in the rubber and plastic industry and is also utilized in pigments, inks, and coatings. In general, virgin CB improves the quality of different products in terms of strength, conductivity, ultraviolet protection, weatherability, etc. Over 75% of the globally produced Carbon Black is used in the tire industry due to its exceptional reinforcement characteristics, among other desirable properties.
Nevertheless, the manufacturing process is criticized as detrimental to the environment due to CO2, SOx, NOx, and particulate matter emissions. In connection with the EU Taxonomy Regulation, Carbon Black production is explicitly cited as contributing substantially to climate change. Therefore, to contribute to the climate protection goal, emissions from the production of carbon black must be reduced.
Economic constraints and environmental issues drive the industry to seek an environmentally friendly and sustainable alternative to virgin Carbon Black (CB). One such material that can substitute virgin CB is recovered Carbon Black (rCB), which is environmentally friendly and sustainable and produced from end-of-life tires (ELT) by chemical recycling routes (pyrolysis).
Recovered Carbon Black is a new category of Carbon Black, produced by thermochemical recycling (pyrolysis) of end-of-life tires (ELT), as it is a heterogeneous nanomaterial comprised of a mixture of more than one grade of virgin CB with varying ash content, particle size, morphology, surface chemistry, and activity. Recovered Carbon Black contains virtually all the inorganics compounds used to manufacture tires (ZnO, SiO2, among others) and several virgin CB grades.
Industrially produced blends of CB with environmentally friendly and sustainable recovered Carbon Black (rCB) have proven their technical and commercial maturity and significantly improved CB's ecological footprint.
The leading tire producers Michelin and Bridgestone manifested their joint interest in rCB at the Smithers Recovered Carbon Black Conference in November 2021 (Amsterdam). [1]
rCB and vCB
The contrasting chemical characteristics and particle morphology of rCB compared to vCB likely hinder rCB's performance in premium applications. vCB has a unique nanostructure and surface chemistry defined by the combustion kinetics during production. In the pyrolysis of ELTs towards rCBs, the organic matter of the rubber compound undergoes decomposition and partly carbonization. It fuses with the original carbon black particles along with other inorganic ingredients. Finally, they all become composite core-shell particles grown around carbon black ‘seeds’ (see Figures 1 & 2).
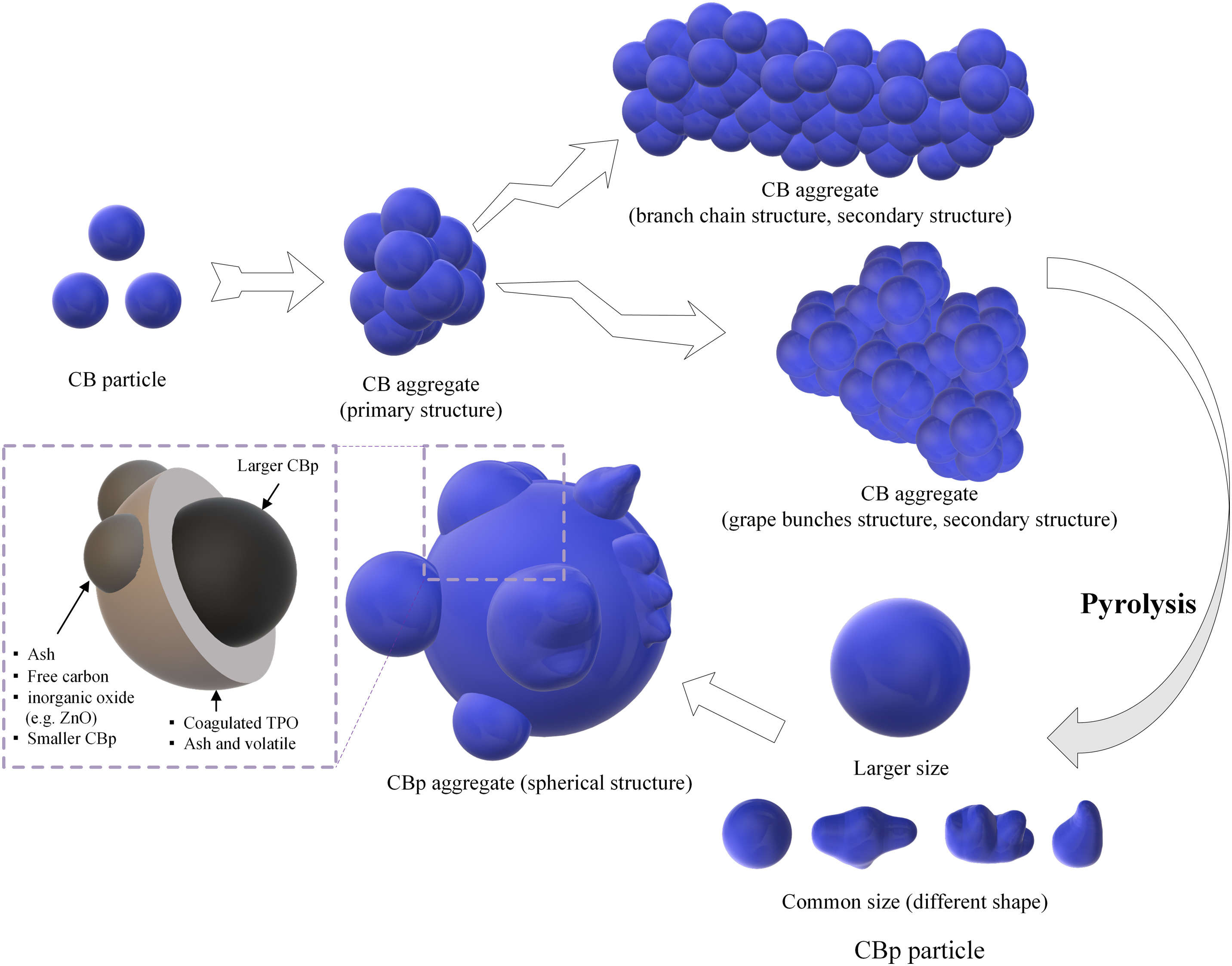
Figure 1: Morphological evolution of carbon black particles during pyrolysis and internal structure model of rCB (CBp) aggregates [4].
rCB particles are typically composed of the following components [3]:
- A wide spectrum of carbon black grades
- Silica, Zinc (S/O), Sulphur
- Amorphous coke layer and organic film from depolymerized bound rubber
Therefore, referring to rCB as "carbon black" may be misleading. Recent insights suggest that rCB is not simply a standard grade of carbon black but a distinct and novel material. [2,3]
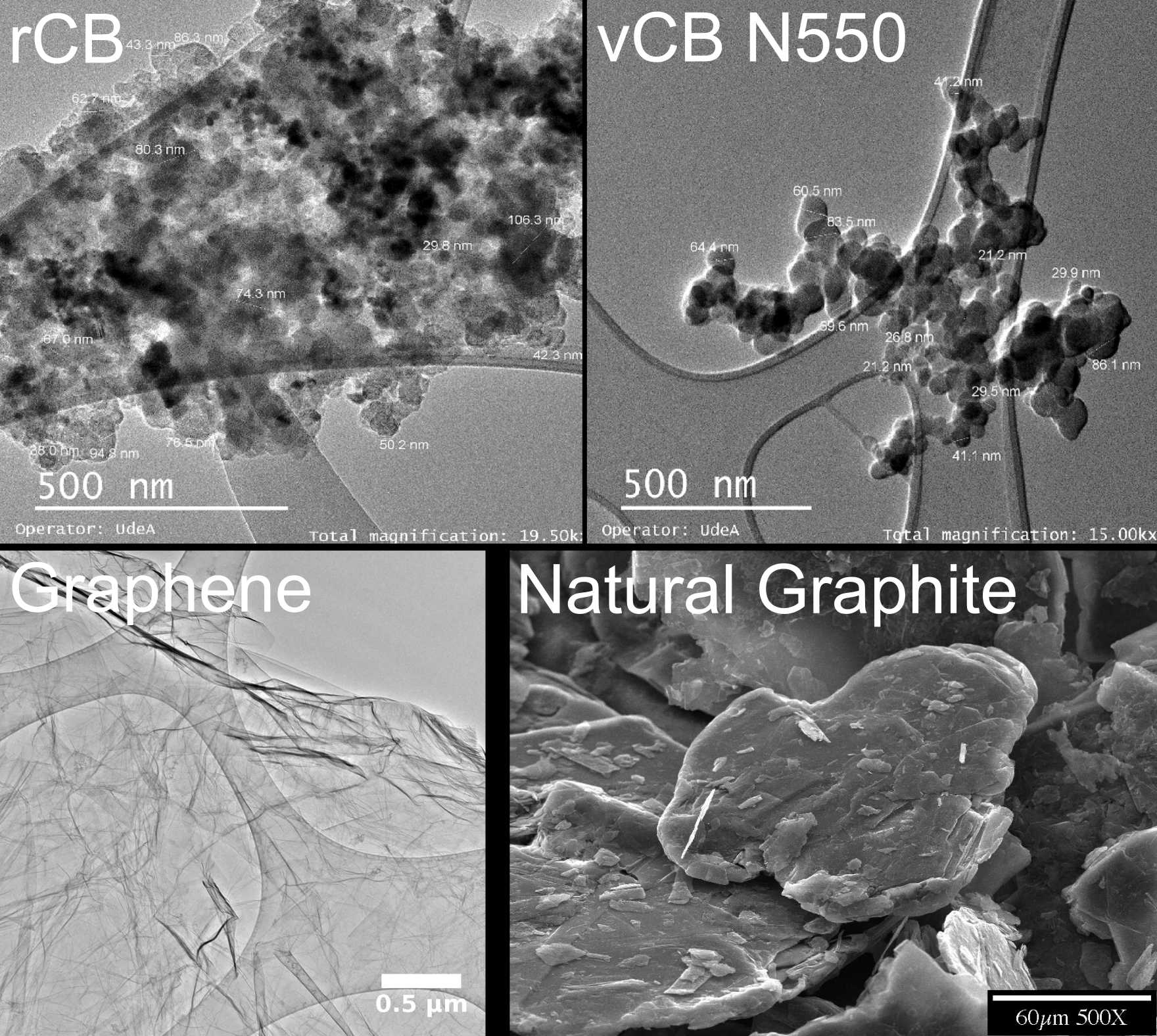
Figure 2: Electron microscopy images of rCB, vCB N550, graphene, and natural graphite. Figure reproduced from references [5-7].
To achieve higher economic value, the ELT pyrolysis industry should consider the complex structure of rCBs as versatile, taking inspiration from other similar “by-products” such as fly ash and not forcing rCBs to be suitable only for certain standard applications. Economically viable routes to commercialization of rCBs should transcend the upgrading and include applications in which:
- rCBs could be used in their original form as pristine as possible or with only minimal post-processing
- rCBs could extend outside the common vCB markets with new use cases of other carbon materials, especially graphite and graphene, considering their technological significance and commercial potential.
Graphite and Graphene
Graphite is a crystalline allotrope of carbon composed of stacked layers of atoms arranged in a hexagonal lattice. Graphite's physical and chemical properties make it industry standard in wide-ranging critical applications, including batteries, refractories, electrodes, metallurgical carburization, casting, and lubrication [8]. Conversely, graphene refers to a single layer of hexagonal carbon atoms as in graphite (See Figure 2). Due to its two-dimensional nanostructure, graphene exhibits exceptional mechanical, electronic, thermal, and chemical properties. Graphene is expected to revolutionize the vast majority of industries and technological sectors.
Despite their almost perfect features, graphene and graphite face serious economic obstacles in their industrial use. Graphite is classified as a critical mineral or strategic raw material in the USA and the European Union since China refines more than 90 % of the world’s natural graphite [9-11]. Graphene production is based on natural graphite or chemical deposition of hydrocarbons, which is still far from full-scale commercialization. Synthetic graphite manufactured by graphitization of fossil feedstock without mining graphite ore is seen as an easy-to-access source. However, synthetic graphite production has considerable carbon and energy footprints. Unfortunately, none of these graphitic substances can be deemed sustainable. Thus, this field presents substantial prospects for accessible, affordable, and sustainable carbon material alternatives.
Many promising engineering scenarios could use rCBs with a performance comparable to graphite and graphene. Although rCBs do not have crystalline 2D atomic structures (as shown in Figure 2), they may still serve as a substitute for graphite and graphene in varying degrees thanks to the compensating effect of the unique chemistry of rCBs. The chemical components of rCBs, carbon, silica, oxides, and sulfides of zinc, are known for their physicochemical synergy and could offset the losses from the deteriorated carbon part. However, the right applications should be carefully identified to benefit from the chemical synergy.
Our scientific research has shown that the following areas are the most promising use cases for replacing graphite and graphene with rCBs:
- Batteries
- Catalysts and Sorbents
- Electromagnetic Shielding
Batteries
Carbon materials, particularly graphite, are essential to all commercial batteries. For example, graphite is the anode used in lithium-ion batteries (LIBs), i.e., virtually every electric vehicle battery. Graphene is also being developed for next-generation batteries. The hybrids of carbon materials, especially graphene, with ZnO and SiOx are actively studied to improve electrochemistry in battery science. Unfortunately, the rCB community still considers these oxides impurities.
Thanks to their inherent chemical characteristics, rCBs are ideal battery materials and generally display better battery performance than graphite. ZnS in rCB transformed from residual ZnO during pyrolysis has a positive effect on the electrochemical performance of LIBs. rCB LIB anode with ZnS impurity delivered a specific capacity as high as 255 mAh/g after 3000 cycles at a current density of 1000 mA/g, a higher reversible capacity than commercial graphite [12]. rCBs were also used as the anode of sodium-ion batteries with good electrochemical stability and capacities of around 200 mAh/g after 100 cycles at a current density of 20 mA/g [13].
Although scientific literature points out that upgrading rCBs to pure carbon may enhance battery capabilities, the current research remains limited and inconclusive. Since the inorganic components of rCBs undeniably contribute to battery performance, rCB composition should be preserved or slightly adjusted to ensure optimum electrochemistry. The pyrolysis industry could find great opportunities by capitalizing on the reduced cost of less upgrading in this scenario for energy storage.
Catalysts and Sorbents
Graphene has been extensively studied as a catalyst in diverse chemical reactions and has exhibited great effectiveness. A common approach to preparing catalysts is to attach metals and metal oxides onto graphene, resulting in synergistic catalytic activity. For example, silica-functionalized graphene oxide/ZnO photocatalyst degraded gaseous benzene with a % removal efficiency of 87% [14]. This indicates that rCB, having a similar composition, may function as a catalyst. The large demand for catalysts and sorbents opens up new avenues for rCBs. The reputation of activated carbon may ease the market entry for rCB.
The ash content (e.g., ZnO, CaO, SiO2, Al2O3, Fe2O3, MgO, and K2O) accompanying rCBs can act as catalysts. Hence, crude rCB was proposed as a low-cost catalyst for tire pyrolysis instead of expensive zeolite, a good example of circularity. By applying rCB catalyst, pyrolytic oil was enriched with valuable single-ring aromatics at a concentration of 50 %. The gas yield increased to 10.5 wt.%, compared to only 3.0 wt.%, in the absence of this catalytic process. The generation of harmful byproducts, especially PAHs, was notably reduced [15]. rCB can also work as catalytic support for metals and metal oxides. Trioxide (CuO-CoO-FeO) loaded rCB decreased the decomposition temperature of ammonium perchlorate from 334.0 °C to 293.2 °C [16].
The physicochemical properties of rCBs enable their utilization as adsorbents and absorbents. Extraction and recovery of rare earth elements are critical because of their technological value. Various adsorbents for rare earth elements have been investigated, yet no material has been adopted for practical use. The adsorption of an aqueous mixture of light rare earth elements (Y, La, Ce, Nd, and Sm) by rCB was compared to commercial carbon sorbents. When tested under various conditions, rCB outperformed other sorbents in terms of adsorption efficiency for all rare earth elements [17].
Electromagnetic Shielding
Radio frequency interference is a fundamental problem in all electronics, usually managed by incorporating electromagnetic shielding materials. Although metals are the earliest and still widely employed option with outstanding shielding properties, their significant mass density, cost, and corrosion risk hinder broader applicability. Carbon-based materials were adopted to address these issues.
Graphite and carbon black are very common in commercial use, but graphene has the highest potential for electromagnetic shielding. Unlike the materials used today, Graphene does not reflect electromagnetic waves but absorbs them at a particularly high rate—99.99% [18]. Metal oxide-graphene composites, especially with ZnO, are actively investigated to enhance shielding effectiveness and tune electromagnetic characteristics [19]. rCBs are similarly supplemented by metals and oxides, which must boost their electromagnetic shielding effectiveness.
rCB was mixed into cement to analyze the electromagnetic and mechanical properties of the cementitious composite. Adding only 0.5 % rCB yielded 24.2 db electromagnetic shielding effectiveness, which is a better result than even some carbon nanomaterials. This would translate into large cost savings in designing products protected against electromagnetic waves. Finally, a small amount of rCB considerably improved the fracture toughness and compressive strength of cement-rCB composites [20].
Conclusion
rCB from ELT pyrolysis presents a significant opportunity for sustainable development in various industries. Its distinct properties from virgin carbon black underscore the need for specialized applications and highlight its potential as a versatile material. While further research is necessary to understand its potential fully, the initial findings suggest that rCB as a multifunctional composite particle can play important roles in advanced purposes. The possibility of rCB as a sustainable substitute for graphite and graphene in batteries, chemical processes, and electromagnetic shielding further emphasizes its value. To fully harness the benefits of rCB, the industry must shift its focus from striving for pure carbon to achieving optimal compositions that maximize performance and environmental benefits. This paradigm shift could pave the way for innovative uses of rCB, contributing to a more circular economy, a reduced carbon footprint, and a better return on pyrolysis investments.
References:
[1] Andreas Kyriakou, Claus Lamer, The promise of pyrolysis in tire circularity: How a maturing industry could change the supply chain, Rubber World, Volume 266, No. 6, September 2022.
[2] Joseph Hallett, Sustainable Carbonaceous Material (SCM) is not Carbon Black, Birla Carbon.
[3] Denise Kennedy, Industry Update on ASTM International Committee D36 on Recovered Carbon Black (rCB), 2024 Tire Recycling Conference Atlanta, GA, May 17, 2024.
[4] Xu, Junqing, et al. "Recovery of carbon black from waste tire in continuous commercial rotary kiln pyrolysis reactor." Science of the Total Environment 772 (2021): 145507.
[5] Cardona-Uribe, Natalia, Mariluz Betancur, and Juan Daniel Martínez. "Towards the chemical upgrading of the recovered carbon black derived from pyrolysis of end-of-life tires." Sustainable Materials and Technologies 28 (2021): e00287.
[6] http://cgm-inc.net/products/
[7] https://commons.wikimedia.org/wiki/File:Graphene_HRTEM.jpg
[8] https://ecga.net/main-uses-of-graphite/
[9] What Are Critical Materials and Critical Minerals? https://www.energy.gov/cmm/what-are-critical-materials-and-critical-minerals
[10] An EU critical raw materials act for the future of EU supply chains https://www.consilium.europa.eu/en/infographics/critical-raw-materials/
[11] Paul Lienert and Nick Carey, Focus: Synthetic graphite for EV batteries: Can the West crack China's code? Reuters https://www.reuters.com/world/china/synthetic-graphite-ev-batteries-can-west-crack-chinas-code-2023-09-12/
[12] Wang, Xuechen, et al. "The positive effect of ZnS in waste tire carbon as anode for lithium-ion batteries." Materials 14.9 (2021): 2178.
[13] Li, Yunchao, et al. "Tire-derived carbon composite anodes for sodium-ion batteries." Journal of Power Sources 316 (2016): 232-238.
[14] Jafari, Ahmad Jonidi, et al. "Synthesis of silica-functionalized graphene oxide/ZnO coated on fiberglass and its application in photocatalytic removal of gaseous benzene." Process Safety and Environmental Protection 116 (2018): 377-387.
[15] Wang, Fengchao, et al. "Investigation of hot char catalytic role in the pyrolysis of waste tires in a two-step process." Journal of Analytical and Applied Pyrolysis 146 (2020): 104770.
[16] Krasnovskikh, Marina, et al. "Recovered carbon black from tires as carbon carrier in metal oxide catalytic systems." South African Journal of Chemical Engineering 49.1 (2024): 64-72.
[17] Smith, York R., et al. "Adsorption of aqueous rare earth elements using carbon black derived from recycled tires." Chemical Engineering Journal 296 (2016): 102-111.
[18] Baltag, Octavian, and Georgiana Rosu. "Applications of Graphite Materials in the Field of Electromagnetic Compatibility." Carbon-Related Materials: In Honor of Nobel Laureate Akira Suzuki’s Lecture at IUMRS-ICEM 2018 (2020): 19-44.
[19] Singh, Ashwani Kumar, et al. "Lightweight reduced graphene oxide-ZnO nanocomposite for enhanced dielectric loss and excellent electromagnetic interference shielding." Composites Part B: Engineering 172 (2019): 234-242.
[20] Mahmood, Ayesha, Rao Arsalan Khushnood, and Muhammad Zeeshan. "Pyrolytic carbonaceous reinforcements for enhanced electromagnetic and fracture response of cementitious composites." Journal of Cleaner Production 248 (2020): 119288.
Weibold is an international consulting company specializing exclusively in end-of-life tire recycling and pyrolysis. Since 1999, we have helped companies grow and build profitable businesses.