Weibold Academy: The superiority of chemical recycling via pyrolysis for end-of-life tires
Weibold Academy article series discusses periodically the practical developments and scientific research findings in the end-of-life tire (ELT) recycling and pyrolysis industry.
This article is a review by Claus Lamer – the senior pyrolysis consultant at Weibold. One of the goals of this review is to give entrepreneurs in this industry, project initiators, investors and the public, a better insight into a rapidly growing circular economy. At the same time, this article series should also be a stimulus for discussion.
For the sake of completeness, we would like to emphasize that these articles are no legal advice from Weibold or the author. For legally binding statements, please refer to the responsible authorities and / or specialist lawyers.
Introduction
Just in February 2023, the Joint Research Council (JRC) of the European Commission [1] published their study results on the environmental and economic factors of chemical recycling (pyrolysis) and energy recovery of end-of-life tires (ELT).
The result of this study in advance: chemical recycling via ELT pyrolysis - including mechanical recycling for feedstock processing - is a more sustainable option for managing ELTs than energy recovery via incineration.
Revisiting a decades-old knowledge
Already in 2010, a much-cited Life Cycle Assessment (LCA) found pyrolysis to be the most eco-effective ELT treatment technology, followed by dynamic devulcanization and ambient grinding. [2] These results were confirmed in 2015 by a Life Cycle Assessment (LCA) study showing that substituting primary resources with pyrolysis products from ELTs provides significant environmental savings. [3]
Furthermore, ELT pyrolysis is classified as environmentally sound management (ESM) within the framework of the International Basel Convention of the United Environment Program (UNEP) since 2011.
Today's pyrolysis technologies have improved significantly, with efficient exhaust gas and flue cleaning facilities, renewable energy sources, and state-of-the-art safety systems, resulting in an even better overall environmental profile. This leads to a greatly increased positive effect on humanity, environment, and resources compared to 2010 or 2015.
Latest findings
The current and very detailed study by the JRC "Environmental and economic assessment of plastic waste recycling" [1] is a comparison of mechanical, physical, chemical recycling and energy recovery of polymeric waste (tyre rubber and plastic).
Exploring the potential of polymeric waste (plastic and end-of-life tires) recycling, this study delves into the environmental and economic benefits of recycling and energy recovery technologies. Mechanical, physical, and chemical recycling options were evaluated, emphasizing the need to prioritize material recovery, minimize processing impacts, and ensure technical and economic feasibility.
Chemical recycling (pyrolysis) of ELTs wins big
This Life Cycle Assessment (LCA) published by the Joint Research Council (JRC) of the European Commission states that the results in net savings for climate change with chemical recycling via (end-of-life tire) pyrolysis but net burdens for energy recovery. However, for particulate matter, acidification, and fossil resource use, both chemical recycling via pyrolysis and energy recovery via incineration provide net savings. [1] Across all three impact categories, chemical recycling (CR) is superior to energy recovery (ER) in terms of net savings.
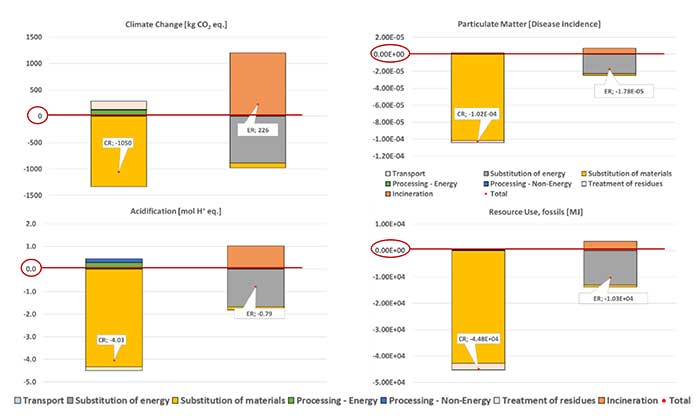
Source (graphic): JRC "Environmental and economic assessment of plastic waste recycling" (pg. 52, Fig. 10) [1] Note: The original graphic was adapted by the author by inserting a more clearly recognizable zero line (red). To explain: bars above the zero line show negative environmental effects, while bars below the zero line show positive effects for the environment.
The graphic above clearly shows that the burdens (bars above the red zero line) from chemical recycling (CR) are relatively small or negligible, as processing and treatment of process residues contribute minimally compared to the savings (bars below the red zero line) from material substitution due to low greenhouse gas emissions from energy consumption. [1]
Carbon black (rCB) and steel provide the most significant savings in material recovery and related substitution credits. It is essential to note that the aggregated nature of the dataset used for modelling the incineration of generic plastic waste makes it impossible to differentiate between burdens and credits in some categories, resulting in "Treatment of residues" as net savings.
The study [1] found that the savings associated with chemical recycling are driven mainly by avoided emissions resulting from material substitution. Chemical recycling avoids the use of fossil fuels to produce virgin materials and instead recovers sustainable secondary raw materials from waste, reducing greenhouse gas emissions.
Additionally, the pyrolysis process for chemical recycling (ELTs) does not require hydro-treatment to upgrade raw pyrolysis oil. This results in relatively low greenhouse gas emissions from energy consumption compared to other pathways.
Overall, the study suggests that chemical recycling via pyrolysis (CR) is a more sustainable option for managing used tyre waste than energy recovery via incineration (ER).
Insufficient data for a correct assessment of the life cycle costing
This section in the current study [1] compares the results of a life cycle costing analysis (CLCC) of managing end-of-life tires (ELT) through chemical recycling with physical recycling and energy recovery scenarios. The costs and revenues of the waste management pathway are categorized into six groups: transport, processing, incineration, treatment of residues, substitution of energy, and substitution of materials.
The analysis shows that incineration of used tire waste results in net savings, while chemical recycling via pyrolysis results in net costs. Which leads the authors of this study to conclude that chemical recycling of ELTs is expected to reach positive net earnings only by 2040.
Unfortunately, this conclusion is misleading and is based on ineffective and long outdated market data. The study correctly points out that insufficient data is available and calls for updating the analysis regarding the economic feasibility assessment.
In general, the study highlights the importance of continually updating and adapting to these emerging advancements to support sustainable waste management policy interventions.
Conclusion
The recent study by the Joint Research Council of the European Commission confirms the long-standing knowledge that chemical recycling through end-of-life tire pyrolysis is a more sustainable option for managing end-of-life tires (ELT) than energy recovery via incineration.
The study shows that chemical recycling provides net savings for particulate matter, acidification, and fossil resource use compared to energy recovery, making it a superior option in terms of net savings across all three impact categories.
Chemical recycling avoids the use of fossil fuels to produce virgin materials and instead recovers sustainable secondary raw materials from waste, reducing greenhouse gas emissions.
While the study highlights the need for updating the economic feasibility assessment due to insufficient data, it also emphasizes the importance of prioritizing material recovery, minimizing processing impacts, and ensuring technical and economic feasibility for sustainable waste management policy interventions.
Our appeal to the ELT pyrolysis industry
Anonymized but real data are essential for accurate study results (also regarding economic factors). With this remarkable study, the objectivity of the study authors is beyond question. It is in the interest of every stakeholder in the entire tire waste value chain to ensure that real and up-to-date data is available to the researchers. If possible, please respond to their inquiries with accurate and complete information. Let us assist you if you would like support in this effort. We will also ensure the anonymity and confidentiality of your data if you desire. Weibold is in the business of deep industry information and known for our loyal and meticulous protection of our clients’ sensitive proprietary information.
Sources:
[1] Garcia-Gutierrez, P., Amadei, A.M., Klenert, D., Nessi, S., Tonini, D., Tosches, D., Ardente, F. and Saveyn, H., Environmental and economic assessment of plastic waste recycling A comparison of mechanical, physical, chemical recycling and energy recovery of plastic waste, Publications Office of the European Union, Luxembourg, 2023, doi:10.2760/0472, JRC132067.
[2] Xingfu Li, He Xu, Yingnan Gao, Yijun Tao, Comparison of end-of-life tire treatment technologies: A Chinese case study, Waste Management, Volume 30, Issue 11, 2010, Pages 2235-2246, ISSN 0956-053X, https://doi.org/10.1016/j.wasman.2010.06.006.
[3] Banar, Müfide. (2015). Life cycle assessment of waste tire pyrolysis. Fresenius Environmental Bulletin. 24.1215-1226.
Weibold is an international consulting company specializing exclusively in end-of-life tire recycling and pyrolysis. Since 1999, we have helped companies grow and build profitable businesses.