Weibold presents highlights of Recovered Carbon Black Forum held in Berlin
As businesses continue to favor sustainable solutions and show commitment to circular economy, it is viable like never before to pay attention to tire recycling and pyrolysis. One of the most outstanding products which is made by means of tire pyrolysis is recovered Carbon Black (rCB).
With recycling and sustainability making headlines in the mainstream news, recovered carbon has ever growing market potential. Its enhanced use would lead to reduction of CO2 footprint, cost reduction to carbon black users, less price volatility and even in some cases performance benefits over carbon black grades. It is used as a substitute for virgin carbon black, or applied in combination with its virgin counterpart; the research of the recycled material’s applications, its blending properties and value is still ongoing, and it was deeply discussed during Recovered Carbon Black Forum held on May 21-22 in Berlin, Germany organized by Smithers Rapra and Martin von Wolferstorff. Moreover, the recent event served as the platform where the current position of rCB on the market, its development and its potential were addressed. Weibold has taken the opportunity to contribute to the forum in Berlin by taking part and sharing knowledge; the team was led by Robert Weibold – consulting expert in the field of tire recycling and pyrolysis, the company’s head, Andreas Kyriakos – senior partner and finance expert with vast international background, and Louis Selinger Romero – key account manager and Market Development Specialist at Weibold focused on market development strategies, technology evaluations and market researches for tire recycling and tire pyrolysis.
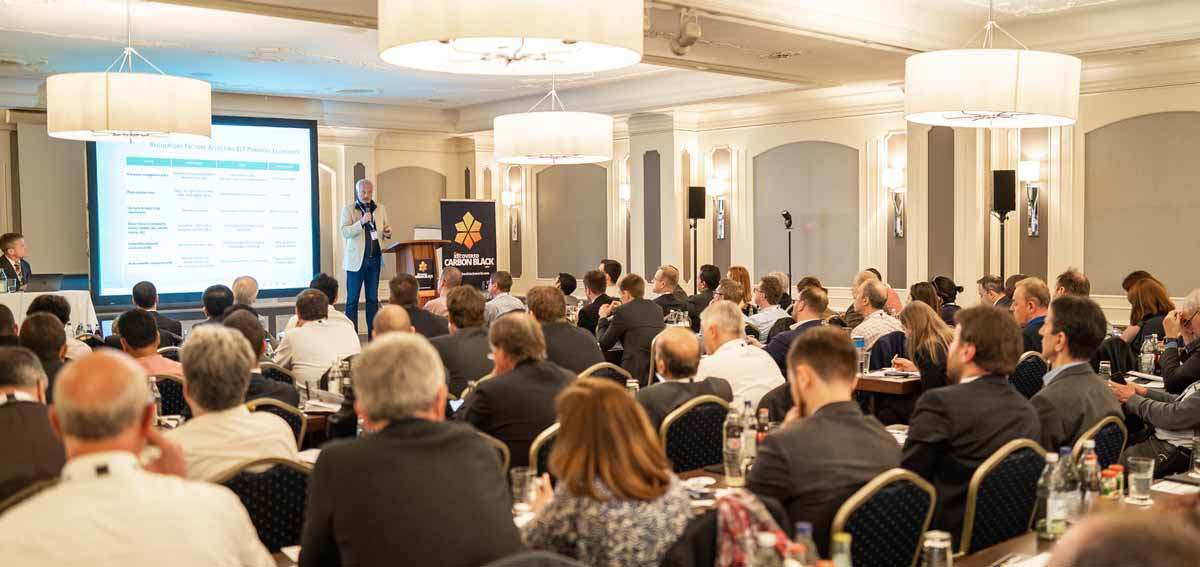
Andreas Kyriakos, Weibold’s senior partner and finacial expert, is explaining economics of running tire pyrolysis business. Photo: courtesy of Recovered Carbon Black Forum.
Currently, recovered carbon black can be attributed to 5% of the global 1.25 billion market. What’s more, now there is a huge demand for sustainable alternatives on the market that could solve the old challenge posed by scrap tires — carbon black can now be successfully recovered from scrap rubber with the help of tire pyrolysis. A substantial contribution to the organization of the forum was made Martin von Wolfersdorff, Owner of Wolfersdorff Consulting, who presented a list of companies worldwide that are now leader in carbon black recovery. He also elaborated on the future of rCB and made his forecasts.
Delivering speech at the Forum, Weibold’s team elaborated on various issues in tire pyrolysis, such as regulatory factors affecting ELT pyrolysis economics, constraints and opportunities for fuel oil, financial aspects of running tire pyrolysis business, investment viability in rCB treatment, etc. Valuable insights were presented by Head of Group Procurement Compounding Materials of Austrian Semperit, Jurgen Heers. Semperit is a company with EUR 900 million turnover who is increasing rCB use in its products — 3% is expected in 2019 compared to only 1% earlier in 2016–2018. As reported by the speaker, the company plans to use over 10% of recovered carbon black in its products by 2022. This sounds ambitious and laudable and could prove to be a great support for the rCB industry.
Currently, Semperit uses the material in production of hoses, rubber sheets and conveyor belts. As reported by the company, some rCB material turns out to lower electric conductivity. In other applications, the manufacturer prefers using rCB in compounds which do not require a specific surface area.
Also, Mr. Heers elaborated on the industry’s expectations from rCB suppliers. Among them are:
- Significant price advantages of rCB compared to virgin material;
- Medium-term price stability;
- Possibility to adjust rCB prices in line with the ones of virgin CB;
- Quality consistency;
- Delivery of custom specifications of material;
- Pelletized material in low melting EVA bags;
- Stable supplies and overall flexibility, etc.
However, he also noted some cons of using recovered carbon black — most of the suppliers are start-ups and they lack expertise in product use. Heers also pointed out that rCB used often includes high ash content.
Similar concerns were expressed by Giorgio Muller, Swedish Hexpol’s representative, who added that it was important to check rCB for PAH content and to make sure that it is sufficiently low – this will help to comply with strict regulations. This view has been echoed by numerous speakers during the forum.
Mr. Muller mentioned that the price of USD 60 per barrel of crude oil is a turning point to successfully market rCB. When oil prices surge over USD 60 per barrel, prices for virgin carbon black increase significantly. To use recovered carbon black in production at Hexpol, a minimum standard of ISO 9001 is required from supplier. The company prefers using “extrusion grades” with low grit content.
One more speaker who addressed the issue of ash content in rCB was Jiri Brejcha, an independent consultant who formerly worked with Mitas/Trelleborg in Czech Republic. He said that the main component of the ash was silica. Providing the solution to the problem, the speaker mentioned that silica should not be treated as ash but as component of the target compound. Brejcha also noted that European tires have higher content of it than US tires. Jakub Szwajka delivered a speech representing Makrochem, a big Polish trader of virgin carbon black with vast blending capacities. According to the speaker, Makrochem is interested blending rCB with conventional carbon black and carries out blending tests in a specialized laboratory.
According to the speaker, in lower quality applications like rubber mats up to 30-50% of conventional carbon black can be replaced by rCB, whereas higher quality applications can bear no more than 15% replacement. Talking about tires, Mr. Szwajka claimed maximum of 5% could be substituted.
Representatives of Neumann & Esser (NEA) touched a topic of production efficiency discussing impact vs. jet mills and asserted that NEA’s impact mills consume max. 50% of energy needed by a jet mill for rCB milling. The Microwave Pyrolysis Panel hosted technology suppliers who discussed numerous issues peculiar to microwave pyrolysis processes, such as better energy efficiency, ease of process control, input requirements, and equipment prices.
ASTM international reported about their trying to standardize testing of rCB which is a very difficult task. It is difficult to compare recovered carbon black with virgin one. Virgin CB can be produced with two types of raw materials derived from petroleum, while the recovered one has a big variety of feedstock and process types. The challenges cannot stop the companies from promoting the use and commercialization of rCB and tire pyrolysis. Most of the participants noted the importance of further research and their commitment to continue studies to develop and upgrade the product using fully equipped labs for testing.
The event proved to be a great success and will take place in such a format again next year.
To see the list of participants, detailed agenda and other information, please consider the official website of Smithers Rapra
Weibold is an international consulting company specializing exclusively in end-of-life tire recycling and pyrolysis. Since 1999, we have helped companies grow and build profitable businesses.