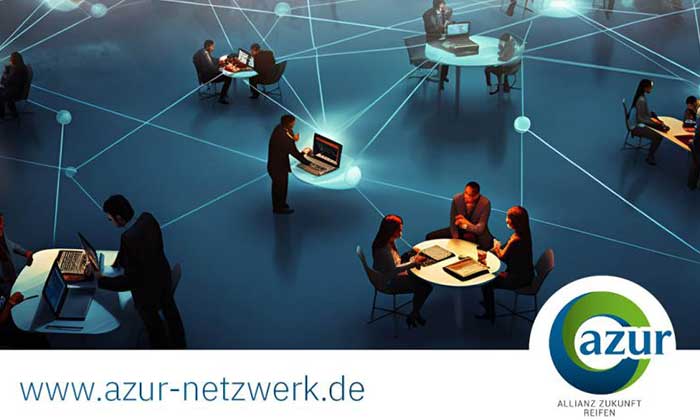
AZuR unveils innovative project group for tire recycling advancements
One of the milestones of the new year for AZuR is the establishment of a new, interdisciplinary project group. The fourth AZuR project group, initially consisting of 11 partners under the leadership of Martin von Wolfersdorff, aims to generate fresh ideas for the chemical recycling of used tires. Interdisciplinary AZuR project groups are intended to advance innovative recycling methods for used tires. Currently, there are already project groups focusing on retreading, material recycling of used tires, and rubberized asphalt. The composition of these groups, with partners from industry, trade, and academia, is chosen to incorporate as many relevant aspects and perspectives on a topic as possible.