Weibold Academy: Need for continued investment in end-use recycled rubber markets
Despite hard efforts of the tire recycling and pyrolysis industry to develop new markets and increase recycling rates, recycled rubber based product markets demonstrate only moderate growth. To tackle the problem and allow thousands of tons of precious materials go back to consumer goods, numerous end-of-life tire management organizations, companies and research labs do their best to find new markets and develop innovative products out of scrap tire rubber.
Current status quo in end-of-life tire markets
While ever more tire recycling plants are launched every year on all continents, the bulk of end-of-life tires still end up as tire-derived fuel (TDF), i.e. incinerated in cement kilns, at pulp and paper factories or at industrial boiler facilities. Despite significant advantages of tire-derived fuel over fossil fuel (mitigation of carbon dioxide emissions), the precious materials contained in tires can be returned to the production cycle if reused and should instead find new use in industrial products and consumer goods.
According to the Scrap Tire Management Report 2019 by the U.S. Tire Manufacturers Association, 4,464 tons of end-of-life tires accumulate in the U.S. annually, out of which some 1,647 tons of ELTs are incinerated as TDF. Good news is that this number decreased by 5% compared to 2017.
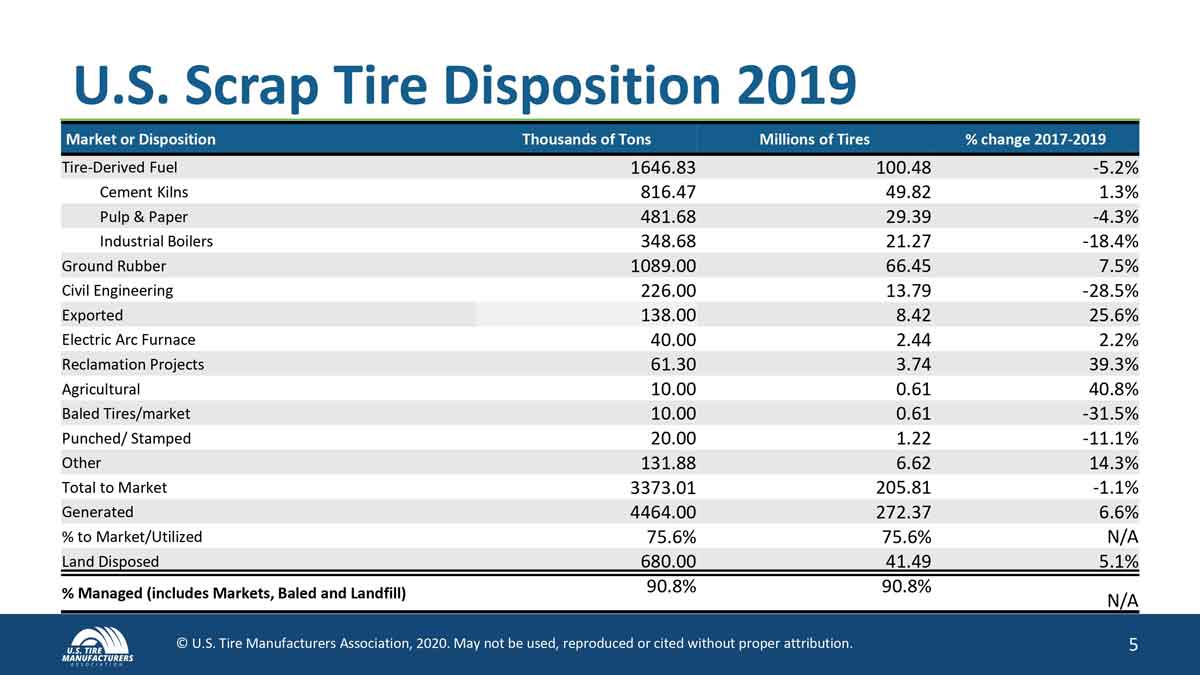
End-of-life tire disposition in the United States in 2019. | Part of 2019 U.S. Scrap Tire Management Report by USTMA.
From USTMA’s statistics we see that the biggest categories for the end-of-life tire use in the U.S. are ground rubber and civil engineering applications. Based on our experience, the distribution in Europe remains similar to that of the U.S.
Unfortunately, the bigger picture looks pessimistic. Recently releases USTMA’s Scrap Tire Management Report reveals that the amount of recycled rubber which finds use in industry and consumer goods has been gradually declining in the United States.
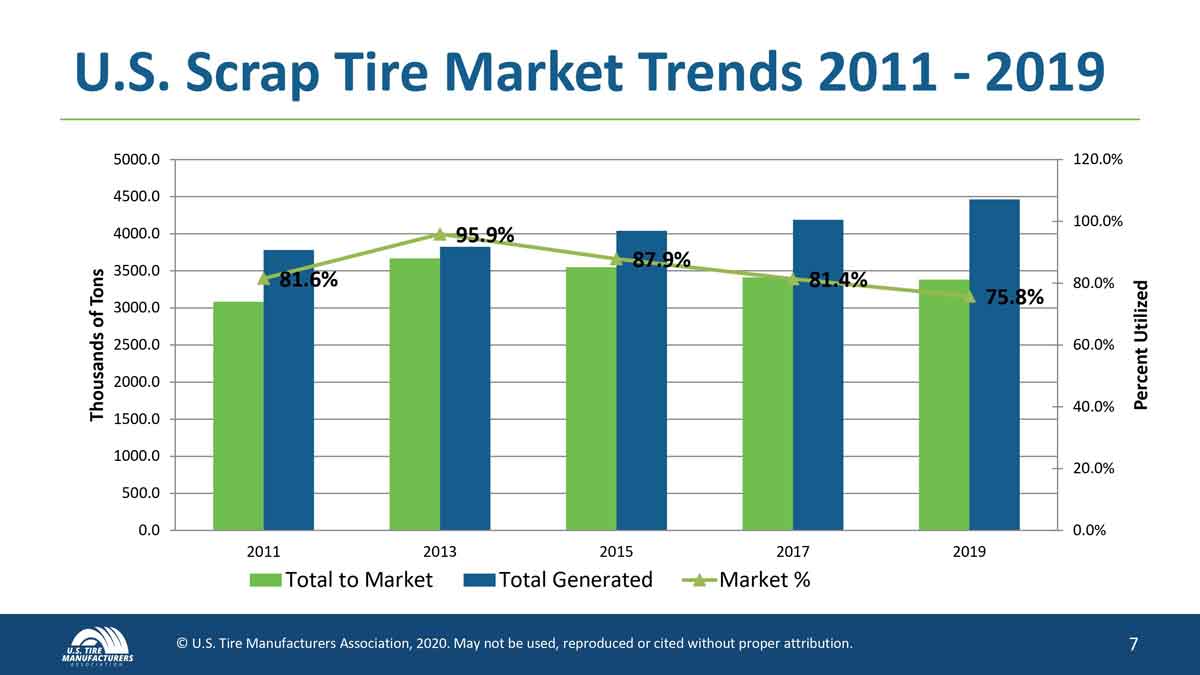
U.S. end-of-life tire market trends in the United States, 2011-2019. | Part of 2019 U.S. Scrap Tire Management Report by USTMA.
Although this is not the case in Europe, the industry needs more R&D, innovation and investments to develop new recycled rubber and pyrolytic end-use products.
Vast market potential of recycled rubber and pyrolytic products
However, a global opportunity has been created by rapidly tightening corporate sustainability goals (CSGs) and the maturing of waste decomposition technologies.
The opportunity shows the characteristics of an emerging and maturing market:
- Demand for consistent, production volume recycled raw materials is on the rise. CSGs are driving major manufacturers world-wide to invest in circular economy concepts by developing new products with rapidly increasing portions of renewed materials. Close cooperation with the recyclers as serious supply chain members is ensuing.
- Equipment designed for thermolytic decomposition of end-of-life (ELT) tires is just now maturing into industrial scale processing suites available from well funded suppliers with scaled production experience of their own. Investment into new pyrolytic and gasification technologies is at an all time high.
- Specifications and accepted testing methods for new raw materials are intensively being worked on by the standards bodies, accelerating the commoditisation of the markets and engendering competition.
Businesses and research labs all over the world succeed in developing innovative products utilizing end-of-life rubber and, taking into account processes that shape the future of end-of-life tires, Weibold concludes that the market is abundant with unexplored opportunities both in tire recycling and pyrolysis.
One of the major breakthroughs of the year is the BlackCycle initiative – a joint project of Michelin, Orion Engineered Carbons, Pyrum Innovations AG, Aliapur and other companies from tire recycling and pyrolysis industry. The project aims at developing innovative solutions to reuse tire-derived materials in tire manufacturing.
According to Michelin, the €16-million project currently involves five research and technology organizations, seven industrial partners and an innovation cluster. Moreover, it spans activities such as tire collection, shredding and granulation, tire pyrolysis, rectification of tire pyrolysis oil into valuable materials, production of recovered carbon black.
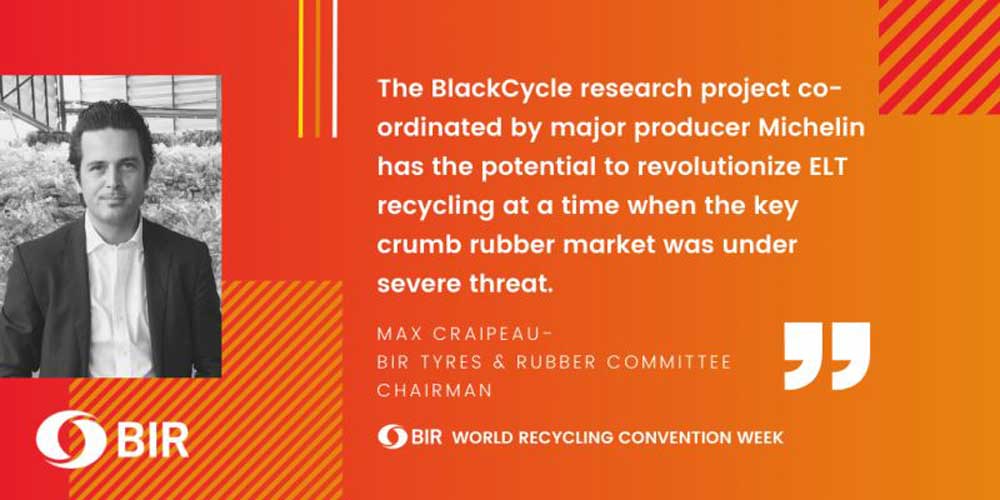
Image: courtesy of Bureau of International Recycling by USTMA.
Other recent examples of breakthroughs in recycled rubber / pyrolysis products include:
- SpaceMat – a Greater Manchester start-up company has launched the first of a range of products aimed at reducing waste from end-of-life tires, supported by the Graphene Engineering Innovation Centre’s (GEIC) ERDF Bridging the Gap program at The University of Manchester.
- Porous pavement surfaces based on recycled tire rubber developed in California and Australia.
- Rubber powder from recycled tires in footwear manufacturing (webinar).
- Protectiflex – innovative spray-on concrete made from used tyres that can protect buildings against blast, ballistics, impact and fire has been short-listed for Australia’s most prestigious manufacturing awards.
- Recyclable self-repairing rubber.
- Rubber devulcanization technologies (e.g. Canadian Phoenix Innovation Technologies or Italian Rubber Conversion winning Keynes Sraffa Award).
- World’s first aerogels from end-of-life tire rubber developed by the National University of Singapore.
- Dry-mix rubber additive to improve rubberized asphalt.
- Other products developed in the recent past allowing to increase profitability of tire recycling businesses with innovative rubber products.
Funding, R&D and market development efforts for the tire recycling / pyrolysis
Even though trends in the U.S. show that the amount of recycled rubber reaching end markets has been steadily decreasing, there has been good news in the industry as well. Today, pyrolysis is regarded as by far the most promising field in tire recycling industry. Below, we list several examples of investments made by either businesses or organizations to help develop market for products from recycled rubber and tire-derived pyrolytic products:
- In late 2020, BASF made a decision to invest in two tire pyrolysis operators as a part of its ChemCycling™ project: German Pyrum Innovations AG and Hungarian New Energy. Supply of pyrolysis oil from end-of-life tires is an important step in the commercialization of BASF’s ChemCycling™ project. Moreover, BASF sees pyrolysis oil from end-of-life tires as an additional raw material source next to oil from mixed plastic waste. The new agreement stipulates that partners will conduct a joint feasibility study that targets the adaption of New Energy’s proprietary pyrolysis technology to the conversion of other plastic waste streams.
- This year, Michelin invested in Canadian plastic pyrolysis operator Pyrowave and formed a long-term partnership with the Swedish tire pyrolysis operator and equipment manufacturer Scandinavian Enviro Systems.
- Successfully running EU-funded project “Silent Rubber Pavements” – novel asphalt additive for better, safer and environment-friendly roads.
- Innovation forum for end-of-life tire recycling launched by German Ministry of Education and Research
- Market development efforts by Tyre Stewardship Australia – the authority has already set up its Market Development Fund that provides assistance to local entrepreneurs. Since the Fund’s launch that took place four years ago, over 30 projects have received financial support.
- Low Traffic Crumb Rubber Road Fund
- Largest rubberized asphalt trial in Australia facilitated by TSA
- Ecopneus signs agreement with Italy’s Army to supply recycled rubber pavement
- SIGNUS helps recycle 185,000+ tons of end-of-life tires in Spain in 2019
- Grants by Australian Federal Government
- Grants by California’s CalRecycle
- Grants for tire recycling in Kentucky
Small contributions matter – support academics and researchers
Often we envision that R&D efforts in the tire recycling and pyrolysis industry should be carried out by big multinational companies with huge budgets, e.g. BASF, Continental, Michelin or others. While this is true that the scale of their activities is large and impact such companies make is tremendous, it is also important to support small initiatives coming from academics.
When the rubber hits the road: recycled tire fibers help create stronger concrete | R&D, project and video by the University of British Columbia.
Today, there are many students and university scholars working on new market applications for recycled tire rubber, pyrolysis oil, recovered carbon black and even tire-derived fibers. Many of the researchers not only look for funding and collaboration with tire recycling / pyrolysis operators, but also utterly depend on them.
If you are running a tire recycling, pyrolysis or a related business, consider supporting young researchers who might need your help to develop a new innovative product. There are many ways of support possible, such as:
- Financial support for the research
- Supplying scholars and researchers with tire-derived materials
- Testing products developed by researchers, etc.
To give you more ideas on how to support researchers and where to find them, we recommend reading an article here. Quick examples include:
- Radar to monitor tire wear developed by American engineers.
- Recycling of waste tire fibers into advanced aerogels for thermal insulation and sound absorption applications.
- Production and droplet combustion characteristics of waste tire pyrolysis oil.
Bright future ahead
Over the last 20 years, tire recycling and pyrolysis gained significant impetus and both fields are expected to grow much more in the coming decade. The demand for recycled tire-derived products is fueled by technology breakthroughs enabling to manufacture recycled rubber based or pyrolysis based products at high quality standards and yet cheaper than their conventional counterparts. Yet in some cases, recycled tire-derived products do not serve as a substitute to virgin material, but help upgrade end-use products’ physical or chemical properties.
The market of recycled tire-derived products is going to grow inevitably in the future, but to fuel and speed up this growth, both big and small stakeholders in our industry need to make concerted efforts, invest and support innovation by cooperating in new product development up and down the supply chain.
Over the last 20 years, tire recycling and pyrolysis gained significant impetus and both fields are expected to grow much more in the coming decade. The demand for recycled tire-derived products is fueled by technology breakthroughs enabling to manufacture recycled rubber based or pyrolysis based products at high quality standards and yet cheaper than their conventional counterparts. Yet in some cases, recycled tire-derived products do not serve as a substitute to virgin material, but help upgrade end-use products’ physical or chemical properties.
The market of recycled tire-derived products is going to grow inevitably in the future, but to fuel and speed up this growth, both big and small stakeholders in our industry need to make concerted efforts, invest and support innovation by cooperating in new product development up and down the supply chain.
Weibold's consulting services in tire recycling & pyrolysis
Weibold has been carrying out market research, pre-feasibility studies, bankable business plans for many years since 1999. To learn more about up-to-date commercial technologies in tire recycling and pyrolysis write us at sales@weibold.com. We have been helping building successful tire recycling and pyrolysis businesses since 1999. Among others, our services include:
Weibold is an international consulting company specializing exclusively in end-of-life tire recycling and pyrolysis. Since 1999, we have helped companies grow and build profitable businesses.